How Our Innovative “Unidrum” Concept Will Shape Future Compactor Design
Here at Volvo, we like to say innovation is in our DNA — that’s because it’s a part of everything we do, from concepts explored at our more formalized Volvo Concept Lab to current product design to blue-sky ideas that have true merit and make their way to market.
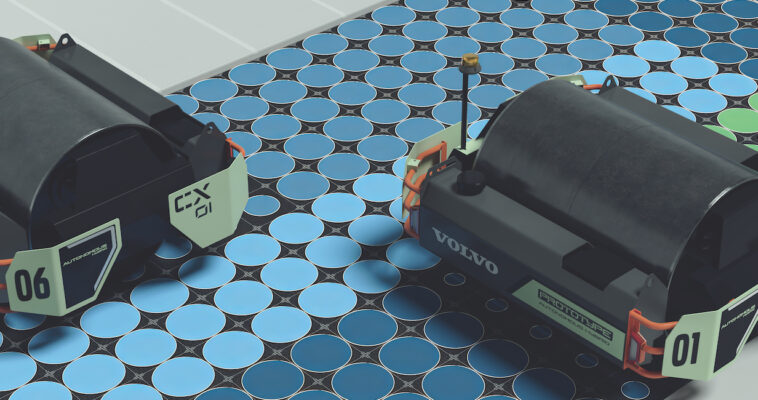
Over the years we’ve developed a number of forward-looking concepts, and the main logic is always the same — What’s possible? What could the future look like? How can we continue to reinvent our machines to increase productivity and efficiency for our customers?
I’m sure it’s exciting for our customers to see new concepts and to hear that we continue to look for ways to improve our product lines — but on a more practical level, it’s exciting and challenging for our engineers to pursue new ideas and technologies that they may not get the opportunity to do under normal development scenarios.
These concepts lead to conversations which oftentimes turn into other ideas, or some portions of the concepts can make their way into future product design. That’s exactly the case with our CX01 compactor concept, which we internally call the “unidrum.” Years of research and development have led to an awe-inspiring concept model that ultimately isn’t planned for market — but many of the learnings out of that endeavor will lead to better asphalt compactor design down the road.
How Does the Volvo CX01 Compactor Drum Concept Work?
The CX01 concept started out as one of those blue-sky type of ideas I mentioned before that generated a “what if?” concept. From there, the idea took on a life of its own. We had several colleagues who were interested in solving problems with unique approaches, and it became a personal challenge to those involved — to see if it was possible.
With the CX01 concept, you have one vibratory asphalt compactor drum that’s actually two independent halves (which we call a split-drum), and it has a control system to self-balance. The unit has a hybrid power train with a small diesel engine and electric motor/battery combo. It can be operated in hybrid or full electric modes. The space for mounting batteries is limited, so for a concept like this to be even remotely viable, it requires an onboard power source to recharge the batteries — thus the diesel engine.
The CX01 concept would offer paving contractors multiple benefits:
– It can operate via remote control or autonomous.
– It lowers fuel consumption and emissions because of the hybrid powertrain.
– It can be “teamed” with multiple CX units to accomplish a job (the units would create a site communication network).
– Units could communicate with trucks and the asphalt plant to coordinate delivery of material, plus jobsite personnel regarding compaction status.
– It utilizes a low-water drum coating to reduce water consumption and asphalt sticking.
A few areas of need that can be explored with this concept are improving the conditions for an operator and increasing productivity. With the CX01 concept, you now remove the operator directly from the unit, so there’s no longer exposure to vibration, noise, dust and other associated environmental conditions. Operators would now essentially play the role of autonomously controlling a fleet of CX units to compact asphalt surfaces.
On the efficiency side, the theory is that a fleet of these units could be deployed on larger jobs where they work together and communicate not only to each CX unit, but to other pieces of equipment on the site. You now have units that can survey the jobsite, report on the conditions of the mat (density, temperature, passes, etc.), and determine when and where to compact.
A Look Inside the Volvo CX01 R&D Process
Everything started with a proof of concept where a drum was hydraulically powered via a remote power source to determine the feasibility of movement and stability. This information was used to refine a design and then construct a physical unit. The physical unit has gone through several design and build iterations to reach its current state.
The initial idea was generated in the U.S., but it was transferred around the globe and back again. We’ve had personnel from the U.S. and E.U. (specifically, Poland and Sweden) involved in the design, build and testing phases.
The design was really based on open communication. In the beginning, there was discussion around what could be done. From that point forward, it became more about connecting those with the abilities and desires to develop the technologies with those that had brainstormed the original ideas. Testing and software refinement is a challenge in and of itself, but that’s more of a digital exercise. The unit either behaves the way that you expect it to or not — and then you iterate.
The other challenging portion of bringing something like this to life was to make it aesthetically presentable. Our industrial design department developed renderings based on the ideas, but these don’t consider all the required cables and small components associated with a working concept. In the end we took a one-off concept unit that was more about function than form and had to deconstruct it, move and modify areas, and then put the pieces back together again.
With a concept like this — developing a system that hasn’t been applied to compaction equipment before — there are always technical challenges to overcome. But this is the nature of this type of work, and it’s something our engineers really enjoy. We want them to feel challenged to look beyond the conventional solutions, to continue learning and to question their own perceptions. Perhaps our biggest obstacle, though, has been available time. This is a project that’s not addressing a direct customer need now, so we’ve had to balance working on this with other priorities that may require an urgent solution.
The CX01 endeavor was purely an exploration. Some learnings could be applied to future products, but there was no expectation that the unit would be more than a one-off investigation.
The reason is that the unit is not practical in its current form. When we develop one-off concept units such as the CX01, we may be using components, mounting locations or design solutions that are different from those that we would use for mass production. Visionary solutions such as the water reduction coating show great potential, but there are no current solutions available in our industry. These are design challenges that can be solved, but ultimately when we look at new products it comes down to what helps our customers do their jobs. If our customers start asking us for solutions like the CX01, anything is possible, and it could go from a one-off concept to serial production.
So how has the CX01 concept already influenced the design of existing asphalt compactors and beyond? We could break down most of the systems on this concept and find ways that just about everything adds tangential value, but if I just pick a few examples, the remote-control system is one. While we’ve previously produced remote control compaction units, the technology continues to improve in all areas, and something like this now could become more practical in other machines. The theoretical coating on the drum shell, while more of a concept on this unit, could prove to be a huge benefit on larger machines to decrease the amount of water needed and potentially the size of the water tanks. This could lead to better sight lines and improved visibility, additional space for mounting other components/systems and more.
Another obvious one is using electric motors and batteries for products such as the L25 Electric wheel loader and ECR25 Electric excavator, even though the components are a little different, and the approach of having a diesel engine or not is different.
The Benefits of a Culture of Construction Equipment Innovation
Whether something like this really sees the light of day isn’t necessarily the driving factor on the engineering side — just getting the opportunity to work with something that’s outside the current status quo is a great way to exercise thoughts and creativity. We’ve had many people from the U.S., Poland and Sweden who have contributed time and effort to this concept, and these types of endeavors are what help keep Volvo equipment at the forefront of innovation and technology, in all markets we serve.
Take a look at our Volvo Concept Lab page to read more about additional machine innovations, new technologies and advanced jobsite setups currently underway with the Volvo Group.
Written by Justin Zupanc – Head of Asphalt Compaction Development Team
Categories: Insights, New Equipment